This dialog allows you to define all of the machine properties required for calculating a project-specific machine hourly rate.
Open Machine Properties Dialog:
- Right click on a project-specific machine ► Properties.
General tab
The General tab contains the master data for the machine - including the name, the inventory number and a description of the machine.
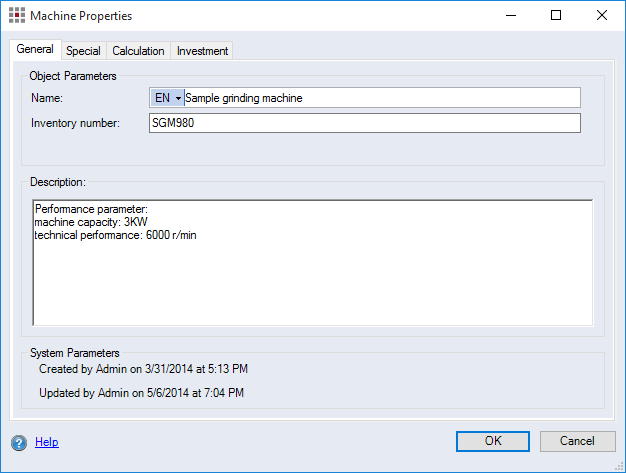
Figure: Machine Properties Dialog, General Tab
Special tab
The "Special" tab enables you to define the machine properties for allocation - e.g. shift model, capacity and performance rate.
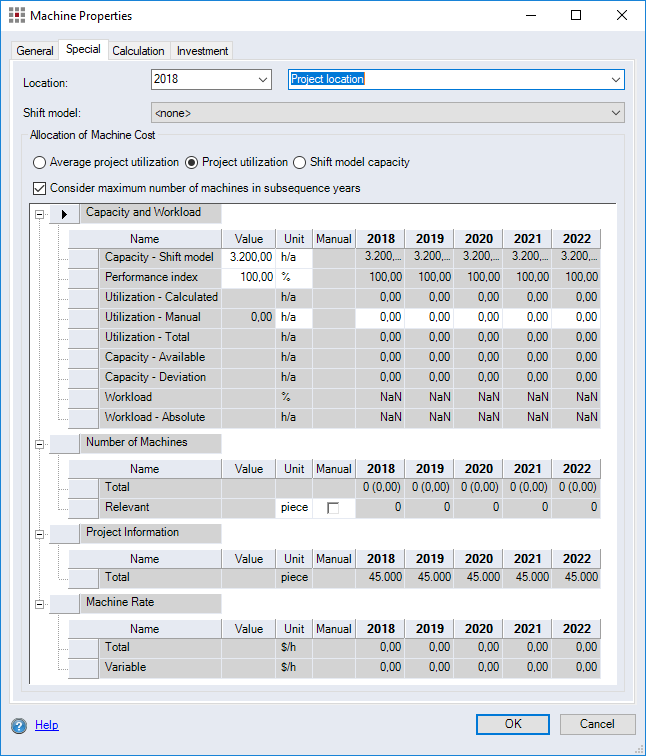
Figure: Machine Properties Dialog, Special Tab
Location selection:
Set the calendar year in the first combobox and the location where the machine is used in the second combobox.
Shift Model combobox:
Set the shift model used for the machine. For machines from Data Administration, the allocated and active shift model is preset.
"Allocation of Machine Cost" group
You can set the method for allocating machine costs in this group and display the calculation parameters for the machine hour rate.
Allocation Options
-
Average project utilization
The allocation is calculated using the average utilization for the machine for the duration of the project. The machine hour rate remains constant throughout the duration of the project.
-
Project utilization
The method "Allocation to project utilization" takes the machine’s actual annual utilization into account. The machine hour rate is calculated for each year.
-
Shift model capacity:
The allocation type listed under shift model is used. If no shift model has been specified, you can enter the value manually into the "Capacity - Shift model" value field.
-
"Consider maximum number of machines in subsequent years" checkbox:
When this checkbox is activated, the number of machines from the year with the highest value in the "Number of Machines, Relevant" row is applied to the subsequent years.
The checkbox can only be activated if the system settings are changed to ensure that the number of machines should be considered for the machine cost rate calculation.
Further Information
Machine Capacity table
This table displays various parameters of the machine hour rate calculation for the duration of the project.
-
"Capacity and Workload" level:
This level shows the machine capacity, utilization and workload for the duration of the project.
-
"Year (bold font)" column: Shows the values of the machine in the current project for each production year.
-
"Year (no bold font)" column: Shows the values of the referenced machine in the external project for each production year.
-
"Capacity - Shift model" row:
Shows the maximum capacity of the machine depending on the shift model in hours per year. The maximum capacity of a machine is an absolute value that describes how many hours a machine can operate per year. The maximum capacity can only be entered manually when no shift model is selected.
-
"Performance index" row:
Shows the percentage factor for the performance rate. The performance rate describes the percentage of the maximum capacity that can actually be used, minus maintenance and downtime.
-
"Utilization - Manual" row:
Displays the manual capacity in hours per year. The manual capacity is an absolute value that describes how many hours a machine is utilized per year.
When activating the checkbox you can manually enter the capacity for the individual production years.
NoteThe manual capacity is used to calculate the machine hour rates when using "Retain the same values when released" for machine references.
For more information, see Select External Projects Dialog.
-
"Capacity - Total" row:
Displays the total capacity in hours per year. The total capacity is determined by multiplying the workload by the available capacity. The total capacity is an absolute value that describes how many hours a machine is utilized per year.
-
"Capacity - Available" row:
Displays the available capacity in hours per year. The available capacity is determined by multiplying the performance rate by the capacity of the machine. The available capacity is an absolute value that describes how many hours a machine can actually be utilized per year.
-
"Capacity - Deviation" row:
Shows the difference in capacity between the total and the available capacity, in hours per year. The utilization is an absolute value that describes how many hours a machine is free per year.
-
"Workload" row:
Shows the percentage of workload of the machine, measured by the available capacity. The machine workload is calculated. You can only enter the workload manually if you have selected the "Shift model capacity" option.
-
"Workload - Absolute" row:
Shows the absolute workload of the machine in hours per year, measured by the available capacity. The machine workload is calculated. You can only enter the workload manually if you have selected the "Shift model capacity" option.
-
-
"Number of Machines" level:
This level shows the theoretical number of machines required for the workload for the individual years – rounded and not rounded.
-
"Position" row:
Shows the number of required machines for the usage point in the project.
-
"Project" row:
Shows the number of required machines for the entire project.
-
"Total" row:
Shows the number of required machines for all references of this machine across all cross-project positions of these machines.
-
"Relevant" row:
Shows the relevant number of required machines. The relevant number is used to calculate the workload and the machine cost rate.
The relevant number can be calculated or manually overwritten (it then corresponds to the total number of machines).
NoteIf you overwrite the relevant number of machines, then changes in the project can no longer be considered when calculating the machine cost rates.
The relevant number of machines cannot be overwritten if the machine cost rate calculation is performed on the basis of shift model allocation or the system settings were not configured to consider the number of machines.
For further information, see Project-specific Machines.
-
-
"Project Information" level:
This level shows the production quantities for the machine per year.
-
"Total" row:
Shows the total quantity for the respective calculation year for all references of the machine.
-
"Project" row:
Shows the total quantity for the respective calculation years in the project.
-
-
"Machine Rate" level:
This level shows the theoretical number of machines required for the workload for the individual years – rounded and not rounded.
-
"Total" row:
Shows the machine hour rate per hour and calculation year.
-
"Variable" row:
Shows the variable portion of the machine cost rate per hour and calculation year from the "Calculation" tab.
-
You can copy the contents of the table and paste them into Excel for editing.
Calculation tab
The relevant costs for machine allocation are defined on the "Calculation" tab.
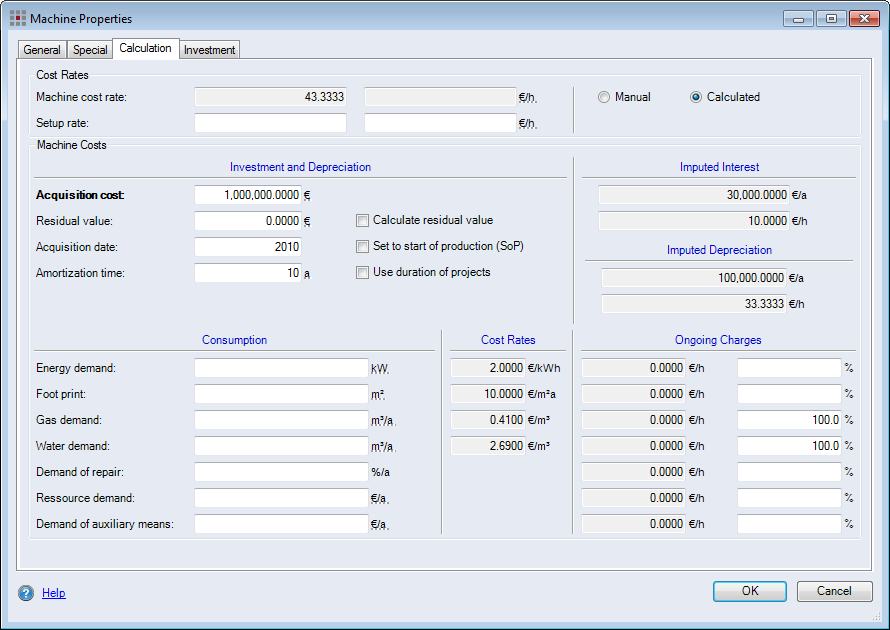
Figure: Machine Properties Dialog, Calculation Tab
"Cost Rates" group
Here you can decide whether manufacturing rate should be calculated or entered manually. The setup cost rate must always be specified manually. The total cost rate is saved in the left text field and the right text field contains the variable cost rate for setup.
Further Information for calculating, see Calculate the cost rate.
"Machine Costs" group
-
"Investment and Depreciation"
The machine's investment costs are indicated in this group.
-
"Acquisition cost" entry/output field:
Enter the costs for acquiring the new machine. If the project-specific machine already exists in the data administration, the current replacement costs are shown.
-
Residual value:
-
Entry/output field:
Enter the residual value of the machine.
-
"Calculate residual value" checkbox:
Activate this checkbox to calculate the residual value. Depending on the default system settings, the residual value is either displayed only or is dynamically considered in the calculation.
Further Information Default Settings Depreciation
-
-
Acquisition date:
- Entry/output field:
Entering the year in which the machine was acquired.
-
"Set to start of production (SoP)" checkbox
Activate the checkbox to use the SOP year as acquisition date.
- Entry/output field:
-
Depreciation time:
-
Entry/output field:
Enter the number of years in which the depreciation takes place.
-
"Use duration of projects" checkbox
Activate the checkbox to automatically calculate the depreciation time with regard to the project lifetime.
-
-
-
"Imputed Interest" and "Imputed Depreciation":
The fixed costs of the machine are determined in the "Imputed Interest" and "Imputed Depreciation" area. To calculate these, data must be entered into the respective fields:
-
"Imputed Interest"
Machine costs can have an imputed interest component. Which means: If a machine was not acquired, this interest could have been generated. The interest costs are added to the costs of the machine.
The first field shows the costs per year and the second shows the costs per hour of the imputed interest. The calculation is based on the interest rate for the linked location of the machine. If no location is linked, no calculation will be carried out and no interest will be charged.
-
"Imputed Depreciation"
The linear imputed depreciation from the replacement costs is calculated without the unallocated share over the indicated years. The costs are calculated for the years of depreciation from the year of acquisition.
The first field shows the costs per year and the second shows the costs per hour of the linear imputed depreciation.
-
"Consumption" group:
Enter the calculation parameters for the machine hour rate costs.
-
"Energy" entry field:
The energy required for the machine.
-
"Footprint" entry field:
Enter the footprint required for the machine.
-
"Repair" entry field.
The share of investment costs required for repairs.
-
"Gas" entry field:
The gas consumption per year.
-
"Water" entry field:
The water consumption per year.
-
"Resource" entry field:
Enter the resource costs per year required to operate the resource.
-
"Auxiliary means" entry field:
Enter the costs of auxiliary materials per year required for operating the machine.
Customize FACTONThe demand and consumption types are configured within the scope of FACTON® Customizing or by an authorized partner.
"Cost Rates" group
The text fields show the cost rates for the respective calculation parameter taken from the assigned location for the machine.
"Ongoing charges" group
Information on the running charges for the respective calculation parameter calculated from the demand and consumption costs along with the location cost rates. The entry fields in the back allow you to enter the variable portion of machine costs in percent.
Investment Tab
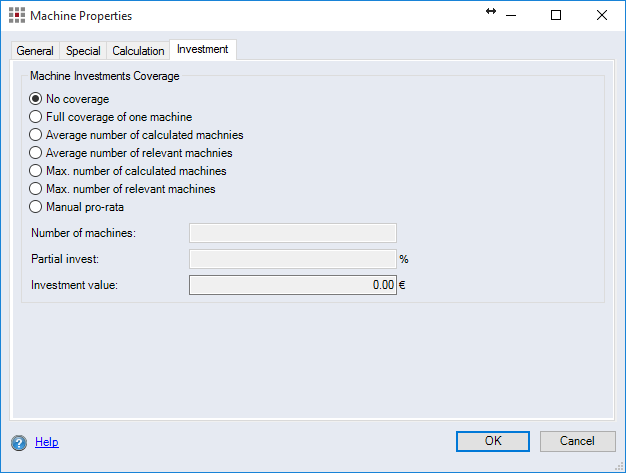
Figure: Machine Properties Dialog, Investment Tab
The "Investment" tab is not available to users who do not have full access rights to the "Capital Efficiency Analysis" function in the Rights Administration Dialog.
"Machine Investments Coverage" group
In this group, define what portion of replacement costs should be included as an investment. The result of the difference of replacement costs and the portion of replacement costs not used in costing is multiplied by a factor you selected in advance. The replacement costs appear in the Investments Category dialog. Machine acquisitions are considered to be cash-out.
-
"No coverage" option:
The surcharge is not included in the investment calculation. There is no additional entry in the investment dialog.
-
"Full coverage of one machine" option:
Total replacement costs of one machine less non-absorbed costs are considered as an investment in the investment calculation.
-
"Average number of calculated machines" option:
The replacement costs are determined based on the average number of machines in the "Number of Machines, Total" row.
-
"Max. number of calculated machines" option:
The replacement costs are determined based on the average value of the calculated machines. The costs are considered as an investment in the investment calculation.
-
"Max. number of relevant machines" option:
The replacement costs are determined based on the average value of the relevant machines. The costs are considered as an investment in the investment calculation.
NoteThe relevant number of machines is a rounded value. It can be overwritten.
-
"Manual input" option:
Define the portion of the replacement costs to be taken into account within the scope of the investment.
-
"Number of machines" entry field:
Input the manual number of machines to be considered in the investment calculation.
-
"Partial invest" entry field:
Enter the share of the machine costs to be considered in the investment calculation.
-
"Investment value" entry field:
Displays the calculated costs to be considered as an investment in the scope of the investment calculation.
-