Costing Scheme
FACTON EPC 9 Should Costing distinguishes between two basic cost types. On the one hand, costs that can be directly assigned to a project element (direct costs) and, on the other, costs that are incurred during production but are not directly tied to a product (overheads).
Further costs can be included in the calculation using additional cost definitions (total lines) on the basis of predefined cost types. These costs are calculated by means of additional total lines per part and/or per product. The total can be calculated either by adding the existing values or by entering a calculation formula. In addition, surcharge rates, such as overheads can be added to all cost elements. Additional surcharges/overheads can also be defined for total lines.
The FACTON product costing scheme consolidates all of the cost types required in total to calculate the complete costing. Costs can be incurred in a project in numerous ways. The chart lists all of the costs that are predefined in FACTON:
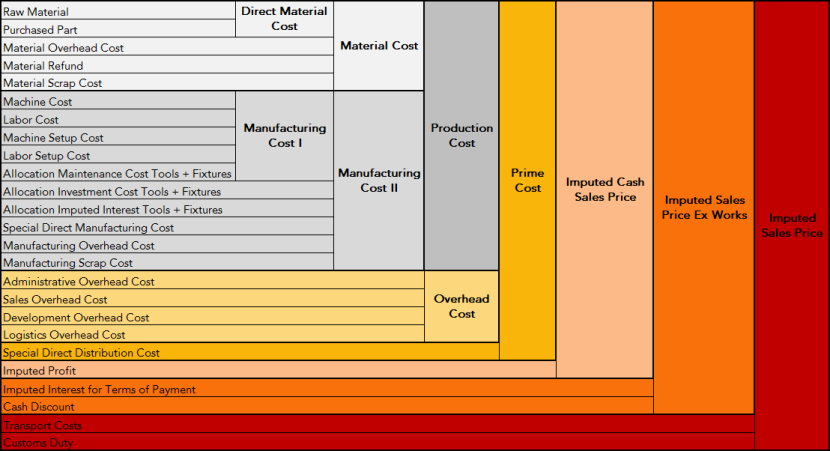
The cost summary in the Details ► Cost Summary view and in the Key Figures view follows this costing scheme.
Note
You can choose the Methodology of your should cost calculation, which is used to determine the following overheads:
- Administration Overheads
- Sales Overheads
- Development Overheads
- Logistics Overheads
These overheads can be calculated based on the Production Costs or the Manufacturing Costs II.
The costing scheme using an example:
Cost type | Sample value [in €] |
---|---|
Direct costs of raw material | 1.00 |
Direct costs of purchased part | 1.00 |
Direct material costs | 2.00 |
Direct material costs of external provisions | 1.00 |
Material overhead rate | 10% |
Material overhead costs | 0.20 |
Material refund | -1.00 |
Material scrap rate | 10% |
Material scrap costs | 0.22 |
Material costs | 1.42 |
Machine costs | 1.00 |
Labor costs | 1.00 |
Setup machine costs | 1.00 |
Setup labor costs | 1.00 |
Allocation maintenance expenses tools + devices | 1.00 |
Manufacturing costs I | 5.00 |
Manufacturing overhead cost rate | 10% |
Manufacturing overhead costs | 0.42 |
Manufacturing scrap rate | 10% |
Manufacturing scrap costs | 0.20 |
Special direct costs for manufacturing | 1.00 |
Allocation investment costs tools + devices | 1.00 |
Allocation imputed interest tools + devices | 1.00 |
Manufacturing costs II | 8.62 |
Production costs | 10.04 |
Administration overhead rate | 10% |
Administration overheads* | 1.00 |
Sales overhead rate | 10% |
Sales overheads* | 1.00 |
Development cost rate | 10% |
Development overheads* | 1.00 |
Logistics overhead rate | 10% |
Logistics overheads* | 1.00 |
Overhead costs | 4.02 |
Special direct costs sales | 1.00 |
Prime costs | 15.06 |
... | 10% |
Imputed profit | 1.51 |
Imputed cash sales price | 16.56 |
Imputed interest for terms of payment | 1.00 |
Cash discount | 1.00 |
Imputed sales price ex works | 18.56 |
Transport costs | 1.00 |
Customs duty | 1.00 |
Imputed sales price | 20.56 |
* Based on the Manufacturing costs It is also possible to calculate this based on the Manufacturing costs II. |