FACTON EPC 22.0 CMD
Cost Model Designer
FACTON EPC Cost Model Designer
Choosing a manufacturing technology in production is also always a question of cost and thus profitability. Different manufacturing processes, various materials and complex parts increase demands on costing. The objective is to evaluate the costs of manufacturing with reasonable expenditure on the basis of valid ratios.
Cost Models Form The Basis of Costing
Companies ensure the validity of their cost accounting using calculation methods – also known as cost models. In this way, costs better reflect the company’s own set of costing rules for a specific manufacturing technology, such as casting, milling or sawing. Cost models facilitate the costing process because product costs are calculated using defined parameters that relate to manufacturing times and material usage based on a recurring pattern.
Companies that lack a standardized costing solution face ever greater obstacles:
- Preparing and/or updating cost models without a centralized costing tool requires a great deal of effort. The data required to do this is distributed across multiple locations and different departments.
- Inputs in locally saved spreadsheets prevent standardized costing because frequently multiple versions exist throughout the company with different information, such as hourly or overhead rates.
- It is virtually impossible to ensure compliance with the set of rules in decentralized units. This can result in non-standardized calculations due to carelessness or a lack of knowledge, for example.
Using the FACTON EPC Cost Model Designer
The FACTON EPC Cost Model Designer (CMD) is a separate module for the FACTON EPC Platform. Cost experts use the Designer to create company-specific cost models via a graphical user interface without the need for programming language.
The FACTON EPC Cost Model Designer prepares cost models in just a few steps:
- The cost-relevant parameters for the component to be manufactured is determined.
- The conditions for cost accounting parameters are defined.
- The BoM structure is specified.
Simpler Costing with Designed Cost Models
The EPC platform supplies pre-designed cost models within the existing FACTON EPC solution, e.g. Should Costing. Users access them directly from within the solution via a drop-down list. An integrated, role-based access control feature makes it possible to give a relevant group of users access to the cost models.
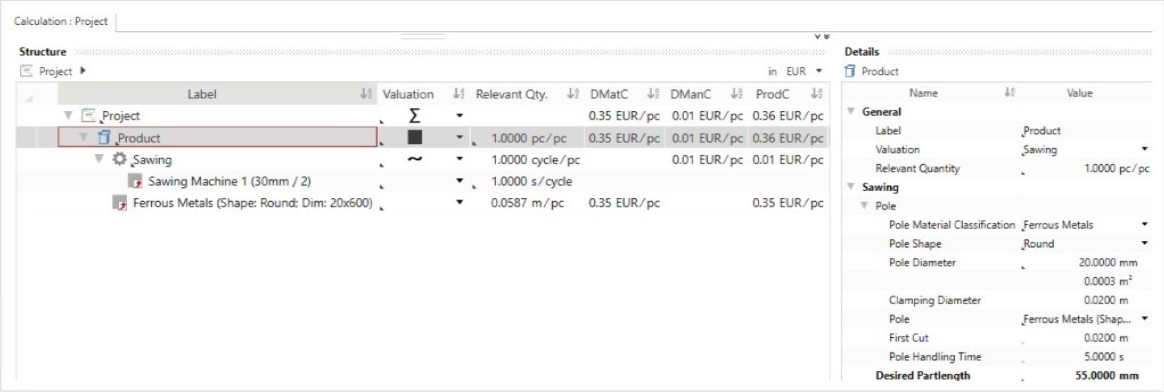
Cost Model created by FACTON EPC Cost Model Designer
Companies can use the cost models to prepare cost calculations to evaluate a manufacturing technology without in-depth technical knowledge. Users need only transfer the manufacturing-related information from the template, e.g. the model drawing. The cost model automatically generates a BoM based on the calculation methods and the designated dependencies.
One advantage: users do not need to build a BoM in order to initiate the calculation. They simply enter the relevant parameters in the summary. The cost model computes the values and prepares the BoM based on the specifications in the model. This provides a clear view of the costs of components, manufacturing steps and material usage.
Quickly and Reliably Analyze Costs using a Solid Database
The FACTON EPC Cost Model Designer helps enterprises standardize their own set of costing rules. The level of standardization remains the same because costing knowledge and specifications are seamlessly integrated in the existing FACTON EPC solution.
Businesses can expand the FACTON EPC solution with their own, in-house knowledge. The iterative costing process is supported because it is no longer necessary to prepare and recompute the cost calculation over and over again. Entering a few key parameters is enough to quickly and reliably analyze costs using a solid database.
Advantages at a glance:
- Efficiency: Costing knowledge is consistently shared with the costing team throughout the enterprise without any breaks in media using the platform-based FACTON EPC solution.
- Transparency: Cost accountants can use the automatically generated BoM to benefit from a high degree of cost transparency, which in turn will help them quickly analyze and identify cost drivers.
- Standardization: Calculations outside of the company’s own set of rules are prohibited and the costing processes – including compliance – are implemented consistently throughout the enterprise.
- Acceptance: A familiar, easy-to-use interface increases user acceptance of cost models. Even non-technical users are able to take advantage of the ad hoc analysis of manufacturing processes.